The safety certifications and standards that sanitary napkin machinery complies with may vary depending on the manufacturer, the specific model of the machinery, and the region in which it is used. Compliance with safety standards is crucial to ensure the protection of operators, meet regulatory requirements, and maintain a safe working environment.
Here are some commonly recognized safety certifications and standards that manufacturers may adhere to:
- CE Marking:
- The CE marking is a certification mark indicating conformity with health, safety, and environmental protection standards within the European Economic Area (EEA). Sanitary napkin machinery intended for use in Europe often complies with CE requirements.
- ISO Standards:
- ISO (International Organization for Standardization) standards related to safety and quality management may apply. For example, ISO 9001 for quality management systems and ISO 14001 for environmental management systems.
- OSHA Compliance:
- In the United States, compliance with Occupational Safety and Health Administration (OSHA) regulations is essential. OSHA sets standards to ensure the safety and health of workers, and manufacturers should adhere to relevant OSHA requirements.
- ANSI Standards:
- The American National Standards Institute (ANSI) establishes standards for various industries, including safety standards. ANSI standards may be applicable to aspects of machinery design and operation.
- UL Certification:
- UL (Underwriters Laboratories) certification ensures that the machinery meets safety and performance standards. UL standards are widely recognized in North America and other regions.
- IEC Standards:
- The International Electrotechnical Commission (IEC) provides standards for electrical equipment, sanitary napkins machinery including safety considerations. IEC standards are globally recognized and may be applicable to electrical components of the machinery.
- GMP Compliance:
- Good Manufacturing Practice (GMP) guidelines are often followed in the manufacturing of sanitary products. GMP ensures that products are consistently produced and controlled according to quality standards.
- Safety Guards and Interlocks:
- Machinery may comply with specific safety standards related to guards, interlocks, and emergency stop mechanisms. These features are designed to protect operators from potential hazards during machine operation.
- Risk Assessment:
- Manufacturers may conduct risk assessments in accordance with relevant safety standards. Risk assessments help identify and mitigate potential hazards associated with machinery operation.
- EMC Directive:
- Compliance with the Electromagnetic Compatibility (EMC) Directive is necessary for machinery that includes electronic components. This ensures that the machinery does not interfere with other equipment and operates safely in its electromagnetic environment.
- Safety Labels and Instructions:
- Machinery should include clear safety labels and instructions in accordance with applicable standards. This helps operators understand proper usage and safety precautions.
- Ergonomics Standards:
- Compliance with ergonomic standards may be considered to ensure that the machinery is designed with operator comfort and safety in mind.
Manufacturers typically provide information about the safety certifications and standards that their machinery complies with in product documentation. It’s important for users to verify the specific certifications and standards relevant to their region and industry to ensure compliance with safety regulations. Additionally, ongoing adherence to safety guidelines and regular training for operators contribute to a safe working environment.
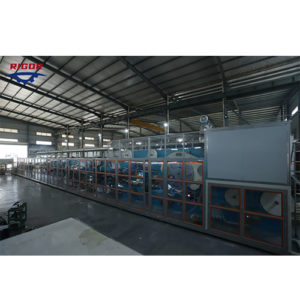