Maintaining and servicing hydraulic valves is crucial for ensuring their optimal performance and longevity.
Here are some key steps to consider:
Regular Inspection: Regularly inspect the hydraulic valves for any signs of leaks, damage, or abnormal wear. Look for fluid leaks around the valve body, fittings, or connections. Check for physical damage, such as cracks, dents, or corrosion. Inspect the valve components, including seals, springs, and spools, for wear or degradation.
Cleanliness: Keep the hydraulic valve and its surrounding area clean. Contaminants like dirt, debris, or moisture can negatively affect valve performance. Clean the valve and its components using appropriate cleaning agents and methods recommended by the manufacturer. Ensure that the hydraulic fluid is also clean and free from contaminants.
Fluid Maintenance: Proper fluid maintenance is essential for optimal valve performance. Regularly check the fluid level and condition, and follow the manufacturer’s recommendations for fluid type, viscosity, and change intervals. Contaminated or degraded fluid should be replaced promptly. Use filters and strainers to remove particles and maintain fluid cleanliness.
Lubrication: Ensure that the valve and its moving parts are properly lubricated. Follow the manufacturer’s guidelines for lubrication intervals and the recommended lubricants. Lubrication helps reduce friction, wear, and corrosion, thereby improving valve performance and lifespan.
Valve Adjustment: Some hydraulic valves may require periodic adjustments to maintain optimal performance. This could include adjusting pressure settings, flow rates, or clearance tolerances. Refer to the manufacturer’s instructions or consult a qualified technician to perform the necessary adjustments.
Seals and O-rings: Inspect and replace worn or damaged seals and O-rings as needed. These components play a critical role in maintaining proper sealing and preventing fluid leaks. Use genuine replacement parts recommended by the valve manufacturer to ensure compatibility and performance.
Professional Servicing: For more complex maintenance and servicing tasks, or if you’re unsure about the proper procedures, hydraulic valve manufacturers it’s advisable to seek the assistance of a qualified hydraulic technician or service professional. They have the expertise and tools to diagnose, repair, and service hydraulic valves effectively.
Remember to always refer to the specific maintenance guidelines provided by the valve manufacturer. Following their recommendations and adhering to proper maintenance practices will help ensure the optimal performance and reliability of hydraulic valves in your system.
What are the advantages of using hydraulic valves in industrial applications?
Hydraulic valves offer several advantages in industrial applications due to their ability to control and regulate fluid flow in hydraulic systems.
Here are some key advantages of using hydraulic valves:
Precise Control: Hydraulic valves provide precise control over fluid flow, pressure, and direction. They allow for accurate adjustment and regulation of hydraulic systems, enabling precise positioning, speed control, and force application. This level of control is essential in many industrial processes that require fine-tuned operation.
High Power Density: Hydraulic systems, including hydraulic valves, offer high power density, meaning they can deliver substantial power in relatively compact sizes. This makes hydraulic systems suitable for applications that require high force or torque output, such as heavy machinery, construction equipment, and industrial presses.
Wide Range of Operating Conditions: Hydraulic valves are designed to operate in a wide range of conditions, including high pressures and temperatures. They can handle demanding industrial environments and provide reliable performance even in harsh conditions. This versatility makes hydraulic systems and valves well-suited for various industrial applications.
Flexibility and Versatility: Hydraulic valves offer flexibility in system design and configuration. They can be easily integrated into complex hydraulic circuits, allowing for customization and adaptation to specific application requirements. Hydraulic systems can be designed for multi-axis motion control, synchronization of multiple actuators, and other specialized functions.
Instantaneous Response: Hydraulic valves provide quick response times, enabling rapid and precise control of fluid flow. This responsiveness is crucial in applications that require immediate adjustments, such as in automated machinery, robotics, and material handling systems.
Overload Protection: Hydraulic valves often incorporate safety features such as pressure relief valves and flow control valves. These mechanisms help protect the system from overloads, excessive pressures, and potential damage. The ability to incorporate built-in safety measures enhances the reliability and longevity of the hydraulic system.
Durability and Reliability: Hydraulic valves are designed to withstand high pressures, heavy loads, and harsh operating conditions. They are typically constructed with durable materials and undergo rigorous testing to ensure reliability and long service life. This durability makes hydraulic valves suitable for demanding industrial environments.
Overall, the advantages of using hydraulic valves in industrial applications include precise control, high power density, adaptability to different conditions, instantaneous response, safety features, and durability. These advantages contribute to enhanced efficiency, productivity, and performance in a wide range of industrial processes.
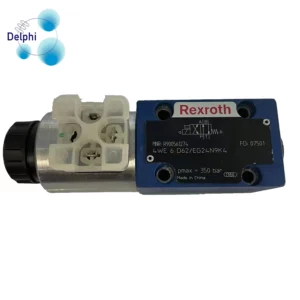