Yes, track rollers require proper lubrication to ensure smooth operation, reduce friction, and extend their lifespan. The specific lubrication requirements may vary depending on the excavator model and manufacturer.
Here are some general guidelines regarding lubrication for track rollers:
Lubricant Selection: Select a lubricant that is specifically recommended by the excavator manufacturer. Different manufacturers may have their own preferred lubricants or specifications. The lubricant should be suitable for heavy-duty applications, provide good adhesion, and have excellent resistance to water washout.
Grease Type: Most track rollers are lubricated with grease. Use a high-quality, lithium-based or calcium-based grease that meets the manufacturer’s specifications. The grease should have the appropriate consistency (NLGI Grade) for the operating conditions and temperature range.
Lubrication Intervals: Follow the manufacturer’s recommended lubrication intervals for the track rollers. These intervals can vary depending on factors such as operating hours, working conditions, and the type of grease used. Regular lubrication is essential to maintain proper lubricant levels and prevent premature wear.
Lubrication Points: Locate the lubrication points on the track roller assembly. These points may be equipped with grease fittings or other access points specifically designed for lubrication. Refer to the excavator’s user manual or manufacturer’s documentation for the exact locations of these lubrication points.
Lubrication Method: Apply grease to the lubrication points using a grease gun or appropriate lubrication equipment. Ensure that the grease is applied with sufficient pressure to penetrate the internal components of the track rollers. Rotate the track rollers during lubrication to evenly distribute the grease.
Quantity of Grease: Apply the recommended amount of grease to each lubrication point. Over-greasing can lead to seal damage or excess grease accumulation, while under-greasing may result in inadequate lubrication. Follow the manufacturer’s guidelines for the appropriate grease quantity.
Cleanliness: Before lubricating the track rollers, remove any dirt, debris, or old grease from the lubrication points. Clean the area around the fittings to prevent contamination from entering the rollers during lubrication.
Inspection: During the lubrication process, visually inspect the track rollers for any signs of damage, excessive wear, or misalignment. If any issues are identified, they should be addressed promptly to ensure optimal performance and prevent further damage.
It’s important to note that the above guidelines provide a general overview, and the specific lubrication requirements may vary depending on the equipment and manufacturer. Always refer to the excavator manufacturer’s recommendations, guidelines, and specifications for the correct lubrication procedures and intervals for the track rollers. Following the manufacturer’s instructions ensures proper lubrication and helps maximize the lifespan and performance of the track rollers.
How can track roller maintenance help extend the lifespan of an excavator?
Track roller maintenance plays a crucial role in extending the lifespan of an excavator. The track rollers are an integral part of the undercarriage system, and proper maintenance can help prevent premature wear, minimize downtime, and enhance overall machine performance.
Here’s how track roller maintenance can contribute to extending the lifespan of an excavator:
Reduced Wear: Regular maintenance, including cleaning and lubrication of track rollers, helps reduce friction between the rollers and the track chains. Proper lubrication ensures smooth operation, minimizes metal-to-metal contact, and reduces wear on the rollers, track links, and other undercarriage components. By reducing wear, the lifespan of the track system is extended.
Enhanced Track Alignment: Track rollers that are properly maintained and adjusted contribute to better track alignment. Misaligned tracks can lead to uneven wear, excavator track link increased stress on components, and decreased efficiency. Regular inspection and adjustment of track roller tension help maintain proper track alignment, reducing strain on the undercarriage and extending its lifespan.
Prevention of Contamination: Track rollers are exposed to various contaminants, such as dirt, debris, and moisture, during operation. If these contaminants enter the roller assembly, they can lead to accelerated wear, corrosion, and damage to internal components. Regular cleaning and removal of debris help prevent contamination and maintain the integrity of the track rollers, prolonging their lifespan.
Early Detection of Issues: Regular maintenance of track rollers allows for the early detection of potential issues or abnormalities. During inspections, worn or damaged track rollers, loose bolts, misalignment, or other problems can be identified and addressed promptly. Timely maintenance and repairs prevent further damage and help avoid costly breakdowns or extensive repairs, increasing the overall lifespan of the excavator.
Optimal Performance: Well-maintained track rollers ensure optimal performance of the entire undercarriage system. Properly aligned and lubricated track rollers reduce friction, minimize power loss, and enhance the excavator’s overall efficiency. This efficiency translates into less strain on the machine, improved fuel economy, and reduced wear on other components, contributing to an extended lifespan.
Resale Value: A well-maintained excavator with a properly maintained undercarriage, including track rollers, retains higher resale value. Buyers and dealers consider the condition of the undercarriage when evaluating used equipment. By demonstrating a history of proper maintenance and care, including regular track roller maintenance, the excavator’s value can be preserved.
It’s important to follow the manufacturer’s guidelines and recommendations for track roller maintenance, including cleaning, lubrication, tension adjustment, and regular inspections. Implementing a comprehensive maintenance program that includes track roller maintenance will help extend the overall lifespan of the excavator, reduce operating costs, and maximize its productivity.
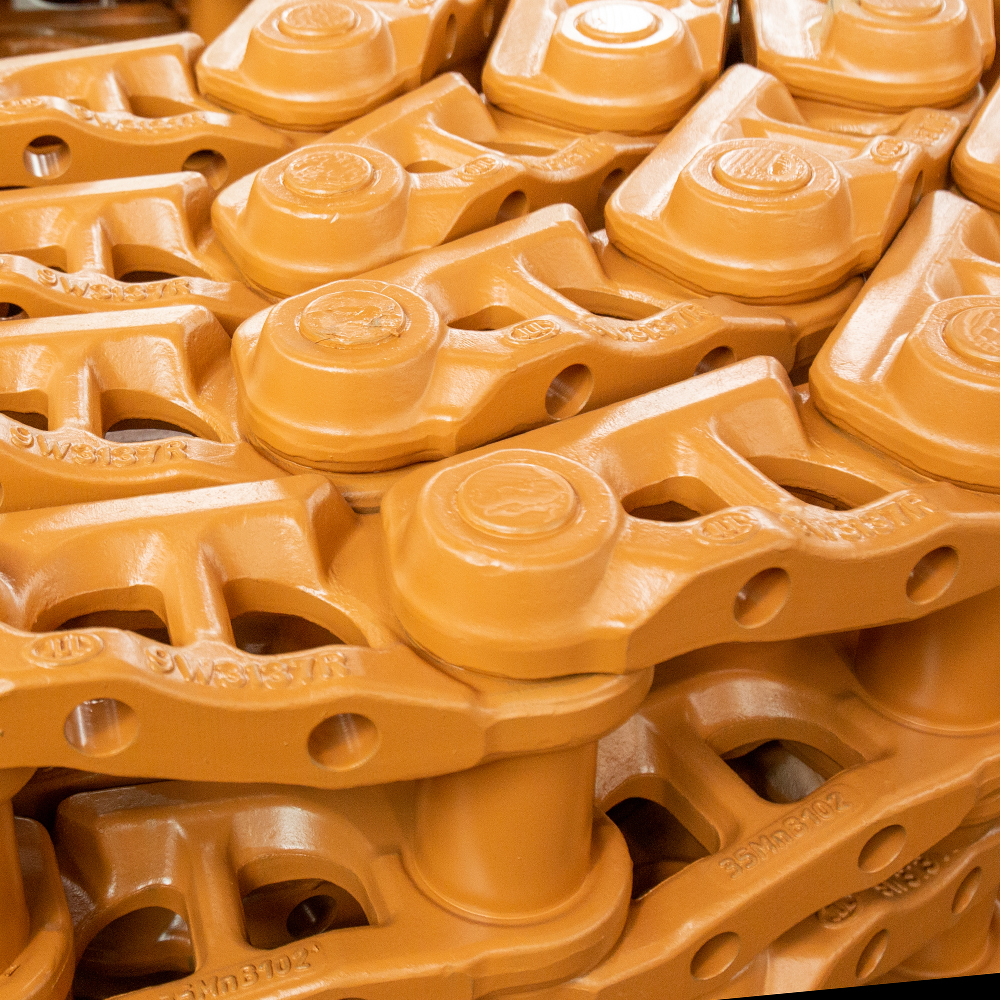